www.industria-online.com
07
'20
Written on Modified on
Un supporto per componenti che sostituisce i circuiti stampati flessibili
I circuiti stampati flessibili offrono numerosi vantaggi. Il fissaggio meccanico di questi circuiti è tuttavia piuttosto complesso. HARTING ha sviluppato una nuova soluzione basata sulla tecnologia 3D-MID, in grado di sostituire i circuiti stampati flessibili. Grazie ai nuovi portacomponenti, è possibile ridurre costi di oltre il 60%.
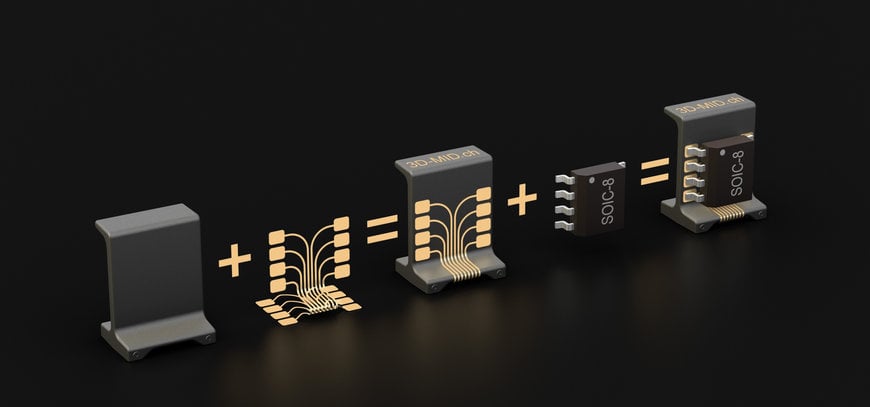
I circuiti stampati flessibili realizzati con sottili film in poliammide si sono affermati in molte aree di produzione grazie alla loro versatilità applicativa. Popolarli e assemblarli è però decisamente più complesso. Ed è qui che entra in gioco il portacomponenti (component carrier) HARTING di nuova concezione.
Un portacomponenti standardizzato per componenti elettronici
Grazie a questo nuovissimo prodotto di HARTING, i componenti elettronici possono essere montati direttamente sul portacomponenti, sostituendo così i circuiti flessibili. Il portacomponenti funge da elemento di connessione tra il circuito stampato (PCB) e i componenti elettronici, come LED, circuiti integrati, fotodiodi e sensori.
I componenti elettronici vengono montati direttamente sul nuovo portacomponenti tramite processi automatizzati. Si evitano così i processi spesso complessi coinvolti nella lavorazione dei circuiti flessibili, ottenendo un risparmio sui costi superiore al 60%.
I portacomponenti popolati vengono distribuiti in modalità "nastro e bobina". Nella versione standard, questi supporti possono essere realizzati all'interno di sistemi di assemblaggio automatico, analogamente ad altri componenti elettronici SMD. Al momento sono disponibili due diversi formati, con la possibilità di ospitare componenti elettronici di dimensioni standard SOIC-8 e anche più piccoli. HARTING offre altresì dimensioni personalizzate su richiesta del cliente.
HARTING ha identificato tre esempi di applicazioni in cui il portacomponenti può sostituire i circuiti stampati flessibili:
- Componenti disposti ad angolo retto rispetto al circuito: il portacomponenti è adatto in situazioni in cui componenti elettrici, come i sensori, devono essere posizionati in senso perpendicolare al circuito. Il processo di assemblaggio automatico permette il posizionamento di sensori di temperatura o sensori hall sul portacomponenti con un elevato grado di accuratezza, che a sua volta si traduce in misure precise e riproducibili. I componenti ottici sono un altro esempio significativo, come i LED o i fotodiodiodi utilizzati per generare barriere luminose precise.
- Separazione dal circuito stampato: il portacomponente consente di mantenere una distanza di separazione tra componente elettronico e circuito stampato. Di conseguenza, un sensore di temperatura può essere utilizzato per misurare la temperatura interna del contenitore senza subire gli effetti del calore disperso dagli altri componenti presenti sul circuito stampato. Ciò implica anche che un LED può essere posizionato lontano dal circuito, evitando così il rischio di ombreggiature da parte di componenti circostanti.
- Funzionamento come antenna: il portacomponenti può essere realizzato utilizzando differenti basi polimeriche. In questo modo, è possibile agire su diverse caratteristiche del materiale dell'antenna, come la costante dielettrica e il fattore di perdita. A seconda del layout, l'antenna può essere impiegata in diverse applicazioni nella banda dei MHz o dei GHz, come Bluetooth, WiFi, ZigBee e 5G.
Tecnologia 3D-MID come alternativa ai circuiti stampati flessibili
Grazie alla tecnologia 3D-MID (dispositivo meccatronico integrato), i componenti elettronici possono essere montati direttamente su un corpo tridimensionale senza la necessità di circuiti stampati o cavi di connessione. Il corpo base è realizzato con stampaggio ad iniezione, mentre il materiale termoplastico è dotato di un additivo non conduttivo e inorganico. Affinché questo materiale possa ospitare circuiti elettrici, gli additivi nella plastica vengono "attivati" con tecnica LDS (Laser Direct Structuring, strutturazione diretta tramite laser). In questo processo, il raggio laser traccia le aree destinate alle piste conduttive e crea una struttura microruvida. Le particelle metalliche rilasciate nel processo formano i nuclei per la successiva metallizzazione chimica.
Questo processo crea tracce elettriche attraverso il corpo base tridimensionale. La plastica utilizzata offre un'elevata stabilità termica e può quindi essere saldata nel forno a rifusione. HARTING implementa direttamente in sede da oltre 10 anni l'intera catena di processo 3D-MID, dall'ideazione del progetto alla produzione della serie popolata. La tecnologia trova impiego in scenari applicativi all'interno di settori come la tecnologia medica, l'elettronica industriale e l'elettronica di consumo, fino a comprendere i componenti relativi alla sicurezza nell'industria automobilistica. La divisione 3D-MID di HARTING rappresenta il principale fornitore di componenti 3D-MID al di fuori dell'Asia. Il portacomponenti sviluppato da questo processo è adatto a svariate applicazioni. Può essere dotato di diversi sensori che, se lo si desidera, possono essere allineati in tre direzioni al fine di eseguire misure su tre assi (X, Y, Z). I componenti possono essere montati simultaneamente su due superfici parallele sui lati anteriore e posteriore, nonché sulla superficie frontale. HARTING ha presentato una domanda di brevetto per il portacomponenti.
Il portacomponenti riduce i costi di due terzi
In un processo automatizzato, HARTING inserisce componenti elettronici come LED, circuiti integrati, fotodiodi e sensori direttamente sul portacomponenti. Il costo totale del portacomponenti è inferiore di oltre il 60% rispetto al costo dei circuiti stampati flessibili. Ciò è dovuto al fatto di poter eliminare la gestione spesso complessa richiesta dai circuiti stampati flessibili, ad esempio nelle operazioni di popolamento, incollaggio e assemblaggio. Il processo è conveniente anche per piccoli volumi di produzione, dal momento che il portacomponenti può essere utilizzato in diverse applicazioni senza la necessità di adattamenti, eliminando così i costi di un nuovo stampo ad iniezione. Rispetto ai circuiti stampati flessibili, questo processo consente un posizionamento più preciso dei componenti, una maggiore ripetibilità e una migliore qualità.
HARTING ha identificato un altro vantaggio del portacomponenti, che è la velocità di consegna dei componenti finiti. Poiché il supporto in plastica resta invariato, tutto ciò che serve sono le specifiche di posizionamento dei componenti elettronici. Gli esperti del processo 3D-MID possono utilizzarlo per proporre layout ottimizzati per la produzione. Le impostazioni del programma laser sono tutto ciò che serve per adattare le tracce elettriche alla rispettiva applicazione. Non appena il cliente ha approvato il prodotto e i componenti sono stati ricevuti, i primi campioni di produzione possono essere spediti entro due o tre settimane, o anche prima, se necessario.
Informazioni su HARTING 3D-MID
HARTING 3D-MID offre l'intera catena del valore delle tecnologie 3D-MID da parte di un unico fornitore, comprso sviluppo e prototipazione di prodotti personalizzati, stampaggio a iniezione, strutturazione diretta tramite laser, metallizzazione, assemblaggio e tecnologia di connessione, nonché verifica finale. Il suo core business è la produzione di componenti meccatronici per il settore automobilistico, l'industria, la tecnologia medicale e i sistemi a sensore. HARTING è il principale fornitore di componenti 3D-MID al di fuori dell'Asia. HARTING 3D-MID è una divisione aziendale di HARTING Technology Group, con sede ad Espelkamp, in Germania.
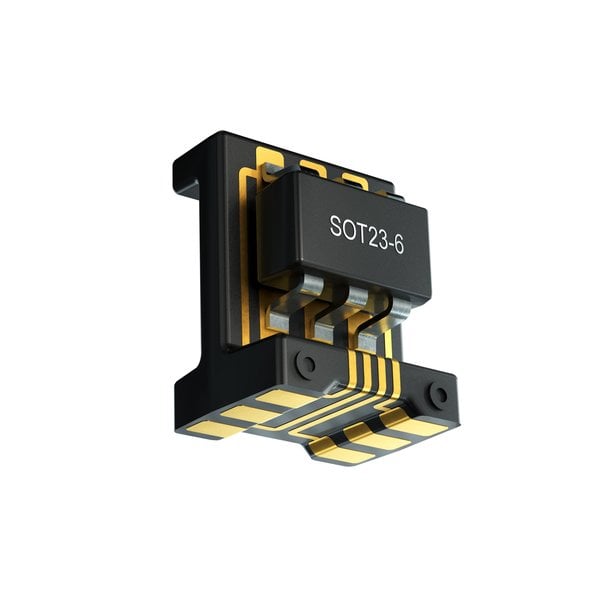
Il formato piccolo del portacomponenti è adatto per componenti di dimensioni SOT23 o inferiori, e misura circa 5 x 4 x 3 mm.
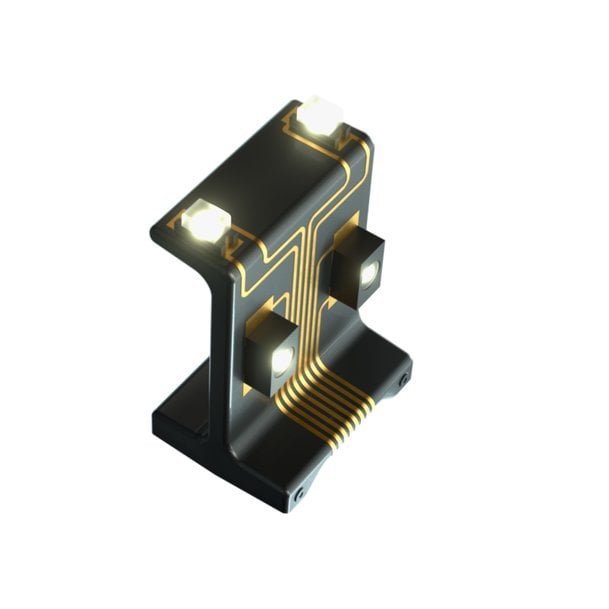
L'immagine mostra la versatilità del portacomponenti. Il portasensori è popolato con componenti elettronici su diverse superfici.
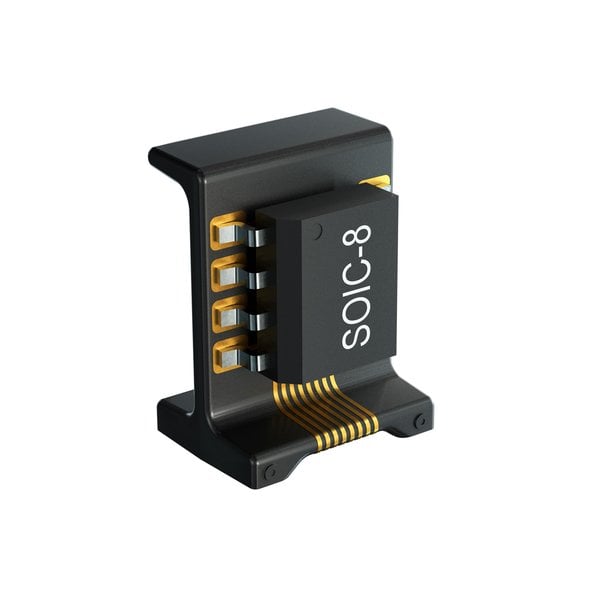
I componenti elettronici vengono montati direttamente sul nuovo portacomponenti in processi automatizzati. Si evitano così i processi spesso complessi coinvolti nella lavorazione dei circuiti flessibili, ottenendo un risparmio sui costi di oltre il 60%.
Richiedi maggiori informazioni…