www.industria-online.com
30
'09
Written on Modified on
Da Tata Steel maggiore qualità e minori costi nelle riparazioni mediante saldatura dei difetti delle rotaie
Tata Steel Rail ha sviluppato una nuova tecnica per la riparazione conveniente di difetti discreti sulla superficie di esercizio delle rotaie. Il punto di forza di questa nuova tecnica risiede nella sostituzione di quegli aspetti del processo Manual Metal Arc (MMA – Arco Metallico Manuale) convenzionale che spesso si traducono nella variabilità della qualità di riparazione, con operazioni automatiche e più controllate. Il processo semiautomatico sviluppato utilizza la saldatura ad arco aperto mediante filo animato con flussante e si basa su una bassa temperatura di preriscaldamento per controllare proattivamente le trasformazioni metallurgiche all’interno della Heat Affected Zone (HAZ – Zona Termicamente Interessata). Poiché il costo medio per la riparazione o la sostituzione di un segmento di rotaia può raggiungere diverse migliaia di euro e il verificarsi di difetti sull’interfaccia fra ruota e rotaia è in probabile aumento a causa dell’evidente incremento dei livelli di traffico sulla maggior parte delle linee ferroviarie, è facile capire l’importanza del nuovo processo.
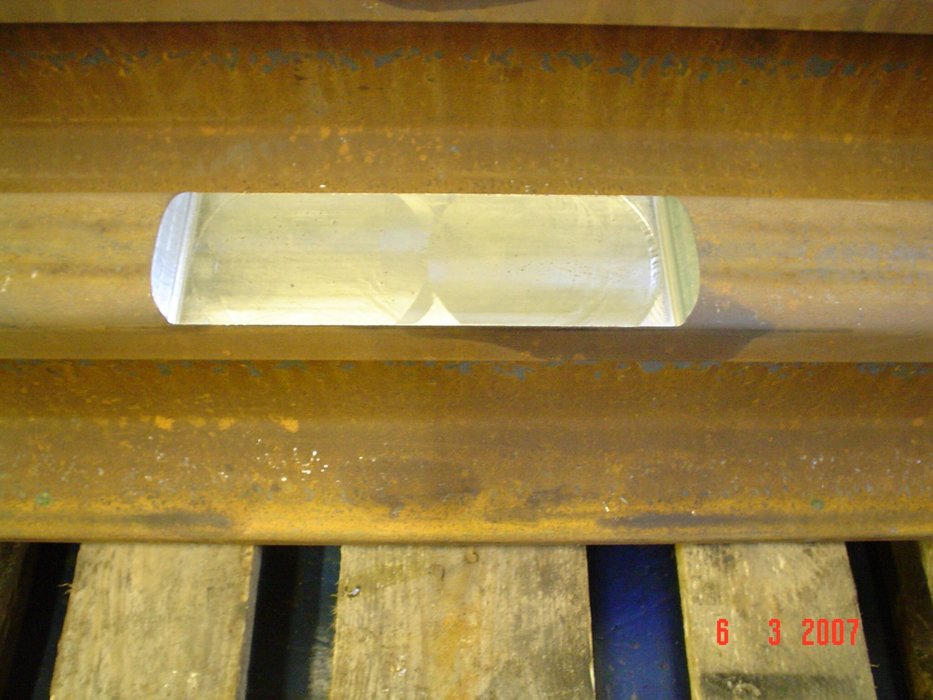
Il processo è stato testato in profondità ed è in corso di costruzione un’unità dedicata per eseguire dimostrazioni sulla linea in diverse reti europee, incluse quelle di Francia e Regno Unito.
Il rotolamento delle ruote dei carrelli sulle rotaie crea pattern di sollecitazione elevati e complessi sull’impronta di contatto fra rotaia e ruota, che si traducono in una degradazione della superficie. L’ampia gamma di conformazioni delle linee, profili delle ruote e tipi di traffico può dare luogo a una varietà di difetti superficiali che riduce la durata delle rotaie. Difetti come ‘squat’ e calcinazione possono verificarsi anche nelle reti ferroviarie più moderne e meglio mantenute e, in linea di massima, ogni rete sviluppa un difetto di questo tipo all’anno, ogni due chilometri. La sostituzione di tali difetti con un segmento di rotaia è costosa e non sempre desiderabile, perché introduce due nuove discontinuità nella linea, sotto forma di due saldature alluminotermiche (reazione esotermica nella quale l’alluminio è agente riducente) che annullano i vantaggi ottenuti con lunghe rotaie laminate a caldo (fino a 120 metri). La tecnica convenzionale alternativa per la riparazione di questi difetti è il processo di saldatura Manual Metal Arc (MMA – Arco Metallico Manuale). Benché tale tecnica sia utilizzata in molti settori industriali, essa dipende pesantemente dalla competenza del saldatore, è laboriosa ed è soggetta a difetti interni come la porosità che può crescere successivamente attraverso la fatica e non viene rilevata dall’ispezione a ultrasuoni, portando alla rottura delle rotaie.
I seguenti fattori contribuiscono alla convenienza economica e alla robustezza tecnica del processo appena sviluppato:
1. L’allontanamento dalla temperatura di preriscaldamento convenzionale di 3500°C a soli 800°C offre i vantaggi di riparazioni più veloci, profondità ridotta dalla zona termicamente interessata e microstruttura più robusta.
2. L’uso di una rimozione standardizzata dell’area di difettosità tramite fresatura controllata ha il vantaggio della riproducibilità ed elimina la valutazione soggettiva dell’operatore.
3. L’uso di un processo di saldatura ad arco aperto semiautomatico programmato mediante filo animato con flussante assicura il controllo dell’apporto termico e tempi operativi prevedibili.
La qualità della superficie di esercizio ripristinata mediante saldatura con il processo sviluppato è assicurata, perché la riparazione è estremamente resistente alla fatica e ha una resistenza di usura simile a quella di una rotaia standard Grado R260 con durezza e microstrutture uniformi sull’area ripristinata mediante saldatura.
La nuova tecnica di riparazione brevettata Tata Steel include quattro fasi.
In primo luogo il difetto viene rimosso utilizzando una fresatrice portatile a tre assi su rotaia che si blocca sui bordi della rotaia e che assicura un’escavazione consistente del difetto identificato. Ciò è di per sé un miglioramento significativo rispetto all’uso della molatura manuale o della discagliatura alla fiamma, entrambe le quali non forniscono una forma della cavità o una finitura superficiale consistenti per facilitare la saldatura automatica programmata.
In secondo luogo, l’area adiacente e la cavità sono preriscaldate con un bruciatore convenzionale. Per le rotaie Grado 260, la temperatura prescritta è fra 60 e 80°C. La scelta di questa temperatura è legata al controllo della microstruttura nell’HAZ e il pattern programmato a onda quadra di deposizione dei cordoni successivi/adiacenti assicura che la microstruttura nell’HAZ sia di perlite fine e libera da ogni martensite causa di fragilità. Questa temperatura è adatta per la vasta maggioranza di acciai per rotaie ad elevato contenuto di carbonio oggi in uso, ma può essere necessario modificarla per acciai che hanno caratteristiche di trasformazione differenti, come gli acciai bainitici privi di carburi a basso contenuto di carbonio.
La terza fase usa una macchina semiautomatica di riparazione mediante saldatura, con processo di saldatura ad arco aperto, un consumabile di saldatura TN3-0 approvato da Network Rail (Regno Unito) e i parametri di saldatura prescritti. Il posizionamento dello strato superiore è cruciale per prevenire la creazione di una nuova Heat Affected Zone (HAZ). La maggior parte degli strati di saldatura superiori è parzialmente rimossa dalla molatura del profilo.
La quarta e ultima fase consiste nel ripristinare e nell’amalgamare i profili trasversale e longitudinale della rotaia mediante molatura, usando molatrici per rotaie convenzionali.
E’ stata ottenuta una valutazione comparativa della tecnica MMA esistente e del nuovo processo registrando la storia termica di entrambi i processi mediante termocoppie incorporate. Numerose conclusioni chiave dimostrano la robustezza metallurgica del processo:
- Nonostante l’uso di un preriscaldamento di appena 80°C, la temperatura nell’HAZ dopo il deposito di ogni cordone di saldatura rimane superiore a 200°C, evitando ogni trasformazione della microstruttura martensitica (poiché la temperatura d’inizio della martensite è di 160°C per le rotaie grado 260).
- Le velocità di raffreddamento nel processo sviluppato sono quasi identiche a quelle del processo MMA convenzionale per tutte le passate di deposito, ad eccezione della prima. La velocità più elevata di 5,2 °C/s dopo il primo cordone di saldatura è anche metà della velocità critica per la trasformazione in martensite.
- E’ evidente un’interfaccia di deposito della saldatura senza cricche, con una microstruttura completamente perlitica, senza martensite e bainite.
- Il profilo di durezza indica che la resistenza all’usura del deposito di saldatura bainitico sarà paragonabile a quello della relativa grado R260 associata, assicurando un buon profilo longitudinale.
- Il deposito di saldatura è stato assoggettato a un test di fatica per piegatura con un range di sforzo applicato equivalente al triplo di quello atteso in servizio. Sono stati completati con successo cinque milioni di cicli senza alcuna rottura. Lo stesso deposito ha sopportato con successo ulteriori 4,3 milioni di cicli con un range di sforzi applicato equivalente a otto volte quello atteso in servizio.
Il rotolamento delle ruote dei carrelli sulle rotaie crea pattern di sollecitazione elevati e complessi sull’impronta di contatto fra rotaia e ruota, che si traducono in una degradazione della superficie. L’ampia gamma di conformazioni delle linee, profili delle ruote e tipi di traffico può dare luogo a una varietà di difetti superficiali che riduce la durata delle rotaie. Difetti come ‘squat’ e calcinazione possono verificarsi anche nelle reti ferroviarie più moderne e meglio mantenute e, in linea di massima, ogni rete sviluppa un difetto di questo tipo all’anno, ogni due chilometri. La sostituzione di tali difetti con un segmento di rotaia è costosa e non sempre desiderabile, perché introduce due nuove discontinuità nella linea, sotto forma di due saldature alluminotermiche (reazione esotermica nella quale l’alluminio è agente riducente) che annullano i vantaggi ottenuti con lunghe rotaie laminate a caldo (fino a 120 metri). La tecnica convenzionale alternativa per la riparazione di questi difetti è il processo di saldatura Manual Metal Arc (MMA – Arco Metallico Manuale). Benché tale tecnica sia utilizzata in molti settori industriali, essa dipende pesantemente dalla competenza del saldatore, è laboriosa ed è soggetta a difetti interni come la porosità che può crescere successivamente attraverso la fatica e non viene rilevata dall’ispezione a ultrasuoni, portando alla rottura delle rotaie.
I seguenti fattori contribuiscono alla convenienza economica e alla robustezza tecnica del processo appena sviluppato:
1. L’allontanamento dalla temperatura di preriscaldamento convenzionale di 3500°C a soli 800°C offre i vantaggi di riparazioni più veloci, profondità ridotta dalla zona termicamente interessata e microstruttura più robusta.
2. L’uso di una rimozione standardizzata dell’area di difettosità tramite fresatura controllata ha il vantaggio della riproducibilità ed elimina la valutazione soggettiva dell’operatore.
3. L’uso di un processo di saldatura ad arco aperto semiautomatico programmato mediante filo animato con flussante assicura il controllo dell’apporto termico e tempi operativi prevedibili.
La qualità della superficie di esercizio ripristinata mediante saldatura con il processo sviluppato è assicurata, perché la riparazione è estremamente resistente alla fatica e ha una resistenza di usura simile a quella di una rotaia standard Grado R260 con durezza e microstrutture uniformi sull’area ripristinata mediante saldatura.
La nuova tecnica di riparazione brevettata Tata Steel include quattro fasi.
In primo luogo il difetto viene rimosso utilizzando una fresatrice portatile a tre assi su rotaia che si blocca sui bordi della rotaia e che assicura un’escavazione consistente del difetto identificato. Ciò è di per sé un miglioramento significativo rispetto all’uso della molatura manuale o della discagliatura alla fiamma, entrambe le quali non forniscono una forma della cavità o una finitura superficiale consistenti per facilitare la saldatura automatica programmata.
In secondo luogo, l’area adiacente e la cavità sono preriscaldate con un bruciatore convenzionale. Per le rotaie Grado 260, la temperatura prescritta è fra 60 e 80°C. La scelta di questa temperatura è legata al controllo della microstruttura nell’HAZ e il pattern programmato a onda quadra di deposizione dei cordoni successivi/adiacenti assicura che la microstruttura nell’HAZ sia di perlite fine e libera da ogni martensite causa di fragilità. Questa temperatura è adatta per la vasta maggioranza di acciai per rotaie ad elevato contenuto di carbonio oggi in uso, ma può essere necessario modificarla per acciai che hanno caratteristiche di trasformazione differenti, come gli acciai bainitici privi di carburi a basso contenuto di carbonio.
La terza fase usa una macchina semiautomatica di riparazione mediante saldatura, con processo di saldatura ad arco aperto, un consumabile di saldatura TN3-0 approvato da Network Rail (Regno Unito) e i parametri di saldatura prescritti. Il posizionamento dello strato superiore è cruciale per prevenire la creazione di una nuova Heat Affected Zone (HAZ). La maggior parte degli strati di saldatura superiori è parzialmente rimossa dalla molatura del profilo.
La quarta e ultima fase consiste nel ripristinare e nell’amalgamare i profili trasversale e longitudinale della rotaia mediante molatura, usando molatrici per rotaie convenzionali.
E’ stata ottenuta una valutazione comparativa della tecnica MMA esistente e del nuovo processo registrando la storia termica di entrambi i processi mediante termocoppie incorporate. Numerose conclusioni chiave dimostrano la robustezza metallurgica del processo:
- Nonostante l’uso di un preriscaldamento di appena 80°C, la temperatura nell’HAZ dopo il deposito di ogni cordone di saldatura rimane superiore a 200°C, evitando ogni trasformazione della microstruttura martensitica (poiché la temperatura d’inizio della martensite è di 160°C per le rotaie grado 260).
- Le velocità di raffreddamento nel processo sviluppato sono quasi identiche a quelle del processo MMA convenzionale per tutte le passate di deposito, ad eccezione della prima. La velocità più elevata di 5,2 °C/s dopo il primo cordone di saldatura è anche metà della velocità critica per la trasformazione in martensite.
- E’ evidente un’interfaccia di deposito della saldatura senza cricche, con una microstruttura completamente perlitica, senza martensite e bainite.
- Il profilo di durezza indica che la resistenza all’usura del deposito di saldatura bainitico sarà paragonabile a quello della relativa grado R260 associata, assicurando un buon profilo longitudinale.
- Il deposito di saldatura è stato assoggettato a un test di fatica per piegatura con un range di sforzo applicato equivalente al triplo di quello atteso in servizio. Sono stati completati con successo cinque milioni di cicli senza alcuna rottura. Lo stesso deposito ha sopportato con successo ulteriori 4,3 milioni di cicli con un range di sforzi applicato equivalente a otto volte quello atteso in servizio.
Richiedi maggiori informazioni…