www.industria-online.com
29
'19
Written on Modified on
La sicurezza al primo posto
Per consentire a esseri umani e robot di lavorare in armonia nelle aree di lavorazione condivise senza alcuna barriera protettiva di separazione, si devono rispettare rigidi requisiti di sicurezza.
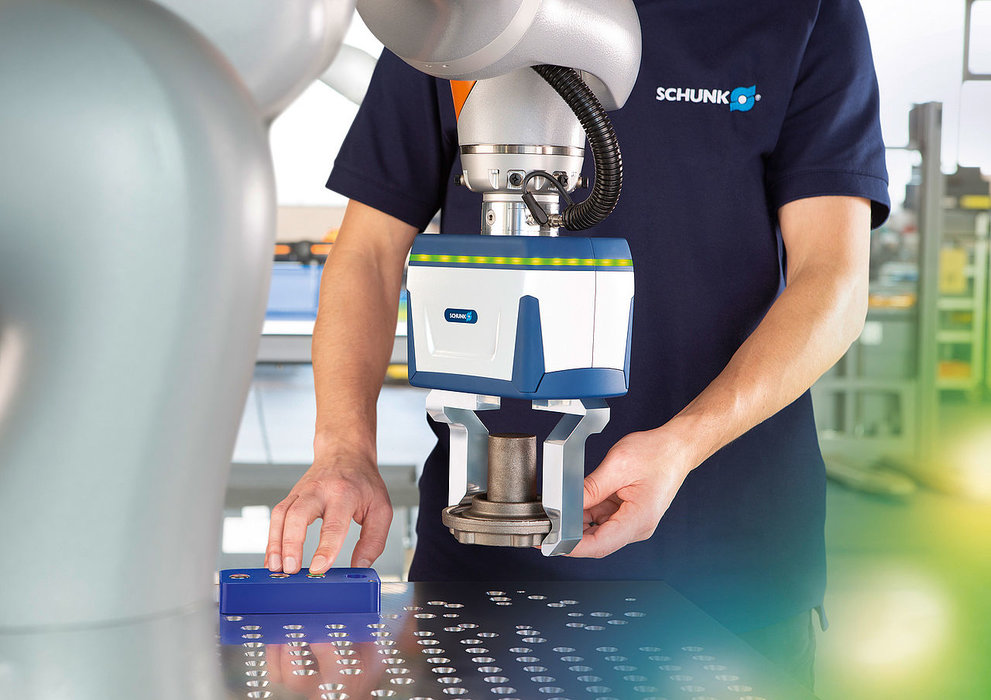
In qualità di produttore di componenti di sistemi di presa certificati HRC, SCHUNK ha deciso in maniera consapevole di considerare in anticipo gli aspetti della sicurezza sul lavoro.
Così facendo, gli aspetti relativi alla sicurezza sono inclusi nei nuovi sistemi di presa fin dall'inizio. Ciò accorcia il processo di sviluppo con componenti standard, abbassa i costi e accelera i progetti HRC per applicazioni specifiche.
"La convalida delle applicazioni HRC rappresenta una sfida particolare," dichiara il prof. dott. Markus Glück, Direttore del reparto Ricerca e Sviluppo presso SCHUNK. Dal lato dell'utente, vi è stata una notevole incertezza su come implementare effettivamente i requisiti di sicurezza e salute sul lavoro sotto forma di linee guida e standard.
"Per favorire la collaborazione sicura tra esseri umani e robot, non è richiesta la sola conoscenza completa dell'applicazione robotica, ma anche una conoscenza specialistica della valutazione del rischio," sottolinea Glück.
Data l'assenza di applicazioni HRC uguali tra loro, è necessaria ogni volta una valutazione individuale del rischio. "Forza, velocità, percorsi di movimento del robot e del pezzo in particolare, inclusi i pericoli derivanti dal trasporto del pezzo."
Questi devono essere entrambi limitati dall'utilizzo di misure di protezione inerenti o, se necessario, dall'utilizzo di misure ulteriori per la protezione dal rischio, ribadisce il Prof. Dr. Glück.
"Il nostro obbiettivo è fornire a costruttori di robot, integratori e costruttori di sistemi componenti maturi e testati in maniera indipendente, utilizzabili per realizzare scenari collaborativi relativamente rapidi e per eseguirne la certificazione."
Serie Co-act certificata
La serie EGP-C Co-act certificata per applicazioni collaborative dimostra ciò nella pratica.
La gamma di pinze comprende quattro dimensioni, è progettata per semplici operazioni di movimentazione ed è installabile, in maniera intuitiva, virtualmente su tutti i comuni robot leggeri come soluzione Plug & Work.
"Con più di 400 installazioni del prodotto attualmente in essere presso clienti e partner, EGP-C Co-act ha dimostrato in maniera sorprendente la sua maturità," dichiara Markus Glück.
La forza di presa che agisce sulla griffa, che vanta una progettazione a sicurezza intrinseca, è limitata a un massimo di 140 N per motivi di sicurezza.
I moduli di programmazione ad alte prestazioni e i plug-in semplificano l'installazione.
Griffe di bloccaggio standardizzate con inserti intercambiabili per l'utilizzo universale semplificano l'ingresso nel mondo della robotica collaborativa da parte dei neofiti.
"Nei luoghi in cui esseri umani e robot condividono un'area di lavorazione, i bordi devono essere arrotondati di modo che gli esseri umani non si taglino nel caso in cui la pinza di passaggio li graffi o preme attivamente contro essi," sottolinea Glück.
"Allo stesso modo si deve evitare l'intrappolamento di dita o pelle". Una chiara visualizzazione della situazione operativa attuale attraverso i LED a colori crea fiducia.
Consultazione durante lo sviluppo del prodotto
Con la EGL-C Co-act, SCHUNK sta compiendo un passo in avanti. Con questo concentrato di forza, per la prima volta in assoluto è stato possibile produrre una pinza per applicazioni collaborative in cui la forza di presa che agisce sulla griffa supera il limite di 140 N considerato non dannoso per la salute.
Come con la pinza collaborativa dai componenti di piccole dimensioni EGP-C Co-act SCHUNK, SCHUNK ha inoltre attribuito grande importanza alla Deutsche Gesetzliche Unfallversicherung (DGUV), accompagnando il processo di creazione del prodotto per la EGL-C Co-act.
Tale collaborazione ha facilitato da subito la comunicazione e il monitoraggio efficiente oltre al rispetto degli standard. Inoltre è stato possibile guadagnare esperienza su come progettare certificazioni e valutazioni della sicurezza di modo che siano intuitive, senza comprometterne la qualità in relazione alla sicurezza.
"Il concetto di sicurezza di questa pinza è altamente sofisticato," spiega il prof. dott. Glück. "Attraverso la tempestiva consultazione durante lo sviluppo della pinza, abbiamo potuto assicurare che, quando si trattava di elettronica di sicurezza, tecnologia di controllo di sicurezza e concetto di sicurezza nell'insieme, venisse dedicata particolare attenzione fin dall'inizio al rispetto degli standard e delle normative giuridiche pertinenti." sottolinea.
Presa in tre fasi
Un sistema di intelligenza di sicurezza sviluppato da SCHUNK, in attesa di brevetto, divide il processo di presa nella EGL-C Co-act in singole fasi.
Fino a quando vi è un pericolo derivante dalla possibilità che le mani o le dita degli esseri umani rimangano intrappolate, il sistema di intelligenza integrato limita la forza di presa a un limite non dannoso di 30 N.
Solo da una distanza dal pezzo superiore a 4 mm, dove non vi è alcun pericolo di intrappolamento, le griffe della pinza si avvicinano con una forza di presa definibile liberamente fino a 450 N.
Se il sistema rileva cedimenti in questa fase di chiusura, per esempio a causa della presa di un pezzo di dimensioni troppo ridotte, e l'operatore desidera rimuoverlo manualmente, allora anche questo movimento sarà automaticamente arrestato.
Lo stesso succede se le dimensioni previste del pezzo vengono superate di 2 mm, quando ad es. nessun componente è disponibile.
Nella terza fase, infine, la pinza rileva se la presa del pezzo è sicura e mette in tensione il freno.
Ne consegue che la EGL-C SCHUNK soddisfa i requisiti per una collaborazione essere umano/robot sicura e garantisce che anche le parti sottoposte a presa, che in presa ad accoppiamento dinamico possono pesare fino a 2,25 kg, non vadano perse in caso di situazione di arresto di emergenza e di relativa frenata completa. Nella presa geometrica, sono anche possibili fino a 8 kg.
Concetto di sicurezza modulare come obbiettivo
Tuttavia quando si tratta di certificazione, rimane ancora molto da fare: "Per far sì che HRC sia all'altezza del suo pieno potenziale, è necessaria una soluzione che consenta a integratori e operatori di realizzare processi collaborativi in autonomia con sforzi ragionevoli. Inclusa la convalida della sicurezza e della salute sul lavoro," sottolinea Glück.
I concetti di sicurezza modulari proposti da SCHUNK, a cui mira con la sua gamma di pinze certificate, possono fornire agli utenti un orientamento e semplificare enormemente la convalida della sicurezza e della salute sul lavoro nei singoli casi.
"Se gli utenti potessero fare affidamento su componenti certificati durante la progettazione di una postazione di lavoro uomo/robot, l'introduzione della collaborazione uomo/robot nella produzione quotidiana potrebbe essere notevolmente più rapida," spiega Glück.
A suo avviso, anche il panorama standard HRC continuerà a svilupparsi ulteriormente. Per esempio la ISO/TS 15066 deve essere revisionata come da specifica tecnica dopo quattro anni al più tardi.
"Per questo motivo è importante che i produttori di robot, i fornitori di utensili di presa e attuatori finali e gli integratori collaborino attivamente con organismi di controllo come il DGUV all'ulteriore perfezionamento degli standard," dichiara Glück.
"In questo caso, gli aspetti inerenti alla sicurezza devono avere la priorità, senza alcun compromesso.
Allo stesso tempo la loro accettazione sarà migliorata quando gli argomenti relativi a sicurezza e semplificazione potranno essere armonizzati durante installazione e certificazione."
Standard e linee guida per la collaborazione uomo-robot
I requisiti giuridici per scenari collaborativi sono inizialmente descritti nella Direttiva Macchine 2006/42/CE allegato 1: il produttore di una macchina o i suoi rappresentanti autorizzati devono assicurare l'esecuzione di una valutazione del rischio al fine di stabilire i requisiti di sicurezza e salute applicabili per la macchina.
Per la valutazione del rischio, l'ambiente immediatamente circostante le applicazioni deve essere incluso nell’analisi.
Tutte le collisioni possibilmente dannose, incluso l'intrappolamento di arti, guanti da lavoro o l'inciampo dell'operatore devono essere prevenute in modo efficace.
I riferimenti normativi per la sicurezza funzionale delle applicazioni HRC, a loro volta, sono standard generali quali la IEC 61508, la IEC 62061 e la ISO 13849-1 e 2.
Oltre a questi, per la sicurezza dei robot industriali si devono prendere in considerazione la ISO 10218-1 e -2.
Nelle specifiche tecniche ISO/TS 15066:2017-04, i requisiti principali di utilizzo per robot in funzionamento collaborativo e dispositivi robotici sono definiti nello specifico.
Questo "standard HRC" descrive le note di utilizzo per quattro tipi di collaborazione e spiega i principi di sicurezza richiesti nel dettaglio.
Contiene inoltre specifiche dettagliate relative alle soglie del dolore da rispettare per le relative aree del corpo.
www.schunk.com
Richiedi maggiori informazioni…