www.industria-online.com
30
'23
Written on Modified on
Smart Factory: una produzione flessibile completamente automatizzata, anche per piccoli lotti
Produzione attiva 24 ore su 24, 7 giorni su 7. Con il cambio automatico dei dispositivi di serraggio di Hainbuch si è ottenuta la massima efficienza per produrre lotti anche di un solo pezzo.

Alla scoperta della Smart Factory di WTO.
Da anni i costi di produzione si dirigono in una sola direzione, verso l'alto, mentre il mercato richiede costi di produzione sempre più bassi. Inoltre, c'è una mancanza di lavoratori qualificati. Queste sono le sfide con cui si confrontano quotidianamente molti produttori, tra cui WTO, un costruttore di portautensili di precisione statici e rotanti. La soluzione sembra ovvia: un capannone di produzione completamente automatizzato. La produzione in lotti è da sempre basata su metodi ben consolidati, ma per le piccole quantità è necessario sviluppare nuovi processi e integrarli in un sistema globale. Perché? Perché i dispositivi di serraggio, ad esempio, devono essere cambiati più volte al giorno, il che pone enormi sfide in termini di processo e sicurezza. In collaborazione con Hainbuch, produttore di tecnologie di bloccaggio di Marbach, WTO ha superato gli ostacoli eseguendo una serie di misurazioni e test strettamente coordinati. Nella nuova Smart Factory di WTO, tutti i processi sono automatizzati, con robot che inseriscono i componenti, cambiano i dispositivi di bloccaggio e sistemi di trasporto senza conducente che portano tutto da A a B. Dalla fine del 2022, la produzione di uno dei componenti degli strumenti guidati funziona autonomamente 24 ore su 24, 7 giorni su 7, in lotti da 1 a 100 pezzi. Si tratta di una pietra miliare per WTO e Hainbuch dopo una fase di sviluppo durata 3 anni.
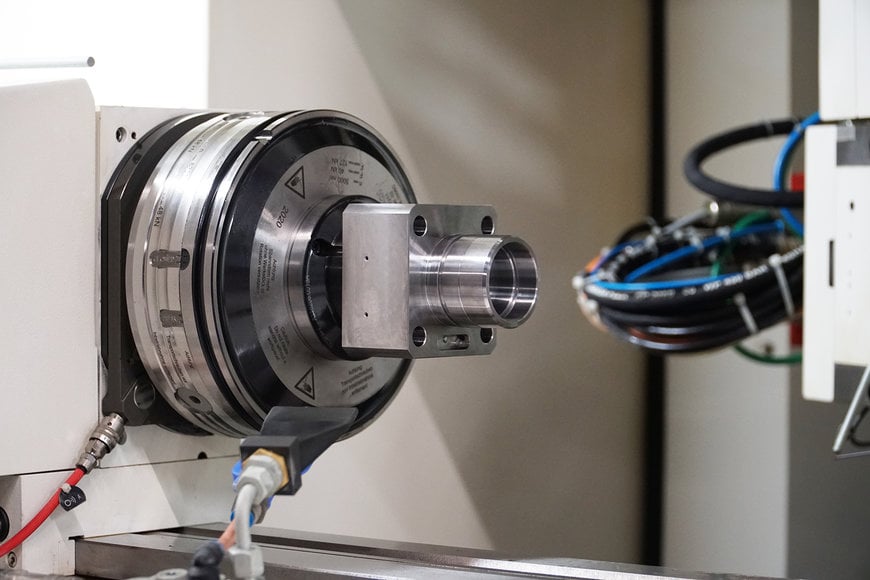
Il pezzo viene bloccato dall'interno su un mandrino ad espansione
La Smart Factory era l'unica soluzione
WTO ha sede a Ohlsbach, vicino a Offenburg, lontano dalle grandi città, dove c'è sempre più mancanza di lavoratori qualificati e, purtroppo, a causa degli sviluppi demografici, questa situazione è destinata a peggiorare. A questo si aggiunge anche il fatto che sempre meno persone vogliono diventare operatori di macchine e c'è sempre meno disponibilità a lavorare su turni. Sascha Tschiggfrei, amministratore delegato di WTO, ha riconosciuto questa situazione e nel 2016 ha iniziato a pensare a delle soluzioni. "I lavoratori qualificati sono una cosa, l'aumento dei costi è un'altra. Poiché operiamo a livello internazionale, la concorrenza è alta, infatti alcune aziende scelgono di trasferirsi all'estero dove i costi sono più bassi. Tuttavia, noi volevamo mantenere la nostra sede in Germania, quindi abbiamo dovuto reagire per assicurarci che la nostra azienda rimanesse competitiva sul lungo periodo. Il nostro futuro è la Smart Factory, che produce 24 ore su 24 e funziona in modo completamente automatico. Ci dà un vantaggio competitivo e ci permette anche di attrarre personale più qualificato", ha dichiarato Tschiggfrei.
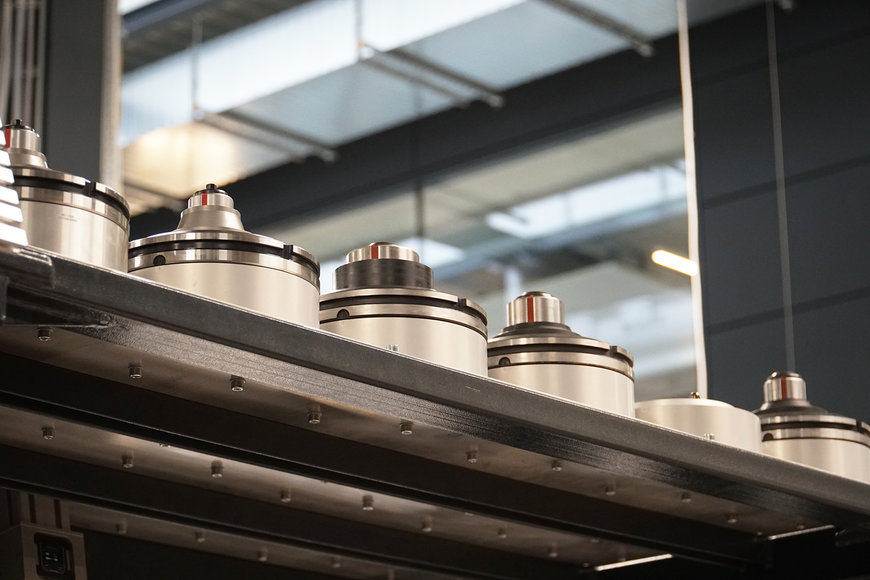
I mandrini pre-attrezzati sono pronti per il cambio automatico del dispositivo di serraggio
La ricerca di un partner esclusivo
Per questo progetto molto ambizioso, WTO voleva coinvolgere un partner esclusivo per le attrezzature di serraggio che, con impegno e competenza, potesse contribuire con una tecnologia adeguata. "Abbiamo elaborato i dettagli tecnici in team di progetto. Le domande erano: come possiamo bloccare i pezzi? Come possiamo automatizzare il bloccaggio? Come possiamo cambiare automaticamente i dispositivi di serraggio? L'obiettivo era che le macchine eseguissero i cambi completamente in autonomia. e ciò richiedeva dispositivi di serraggio che avessero questa capacità. Inoltre, avrebbero dovuto rispettare il processo di rettifica ad alta precisione che utilizziamo regolarmente, con una tolleranza massima di 3 µm", ha dichiarato Tschiggfrei. Una volta definito il concetto di Smart Factory, il passo successivo è stato quello di cercare un partner. Poiché WTO e Hainbuch avevano già collaborato con successo in vari progetti internazionali, Hainbuch è stata la prima scelta. Alla fine del 2019 sono iniziate le prime discussioni per definire i requisiti del dispositivo di bloccaggio e le proposte di design sviluppate da Hainbuch sono state accettate.
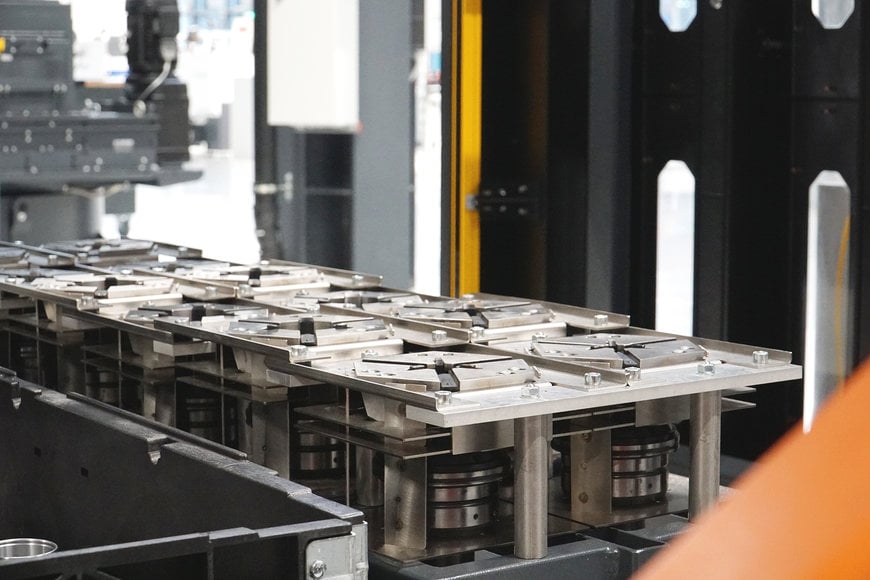
Per la produzione di diversi alloggiamenti, sono disponibili 18 set di serraggio, ciascuno composto da una pinza di serraggio con battuta d’appoggio
Pronti a partire
WTO dispone di un capannone di produzione con oltre 50 macchine CNC. Il serraggio su queste macchine veniva effettuato principalmente con mandrini a griffe e sia il cambio che l'allineamento per ogni postazione erano effettuati manualmente. Il primo processo di produzione completamente non presidiato implementato nella Smart Factory è stato la produzione di un alloggiamento, con una lavorazione soft seguita da una lavorazione hard. Tschiggfrei ha spiegato ulteriormente: "Le macchine della Smart Factory sono tutte nuove. Si tratta di macchine standard, ma adattate in modo specifico per consentire il cambio automatico dei dispositivi di serraggio mediante un robot". Hainbuch doveva equipaggiare quattro macchine con dispositivi di serraggio: due centri di tornitura/fresatura in una cella con bloccaggio interno sul contro-mandrino e due rettificatrici cilindriche in un'altra cella, una con bloccaggio esterno e una con bloccaggio interno. Per il serraggio esterno per la rettifica, Hainbuch disponeva già di un mandrino standard, il TOPlus AC 100 con effetto di tiro assiale. Per i vari alloggiamenti sono ora disponibili 18 set di bloccaggio, composti da una pinza di serraggio con battuta d’appoggio, che vengono sostituiti automaticamente nel mandrino. Tuttavia, per il serraggio del diametro interno durante la tornitura e la rettifica, è stato necessario uno sviluppo completamente nuovo. Ci si è basati sul mandrino ad espansione MAXXOS T211 esistente, e ne si è sviluppato uno speciale implementando i controlli di sicurezza.
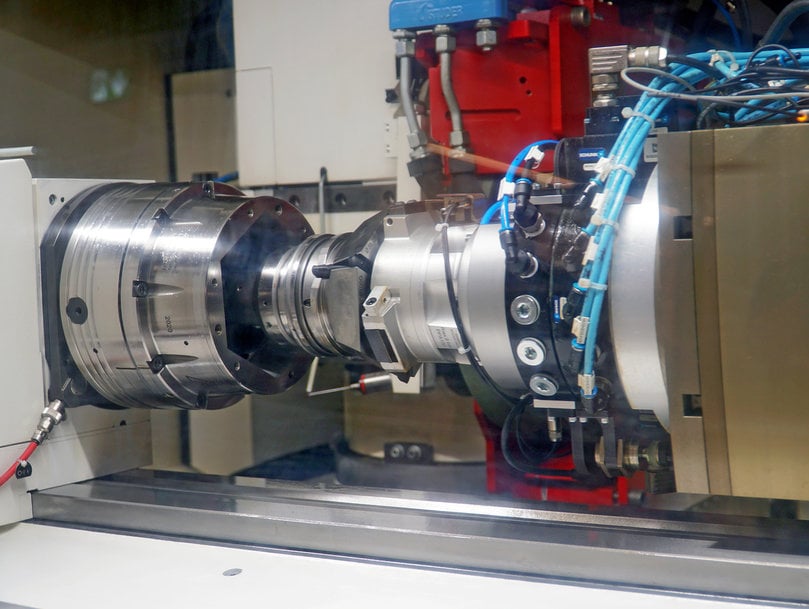
Rigorosi requisiti per i dispositivi di serraggio
Per Björn Schiesling, ingegnere progettista del reparto automazione di Hainbuch e che ha partecipato fin dall'inizio a questo nuovo progetto, ci sono dei requisiti fondamentali che devono essere considerati nell'automazione. "Cosa manca al cambio automatizzato dei dispositivi di bloccaggio? Il dipendente che pulisce le superfici di contatto. Anche le più piccole particelle di sporcizia causano una perdita di precisione. Poi ci sono i controlli di sicurezza: il mandrino può ruotare? È teso correttamente? È posizionato correttamente? È possibile che qualcosa si allenti? In generale, tutte cose che normalmente vengono controllate e regolate dall'operatore, ma con l'automazione non è più così. Per noi è stata una grande sfida implementare questi controlli nei dispositivi di serraggio. Naturalmente, abbiamo anche dovuto capire con il costruttore della macchina utensile come questo processo potesse essere implementato in termini di tecnologia di controllo, monitorando la posizione della corsa. Ad esempio, per il controllo attraverso il rilevamento dell'aria, abbiamo creato i canali nel dispositivo di bloccaggio in modo da poter implementare l’automazione, ma è stato il costruttore della macchina ad installare l'alimentazione dell'aria e i sensori che comunicano con il sistema di controllo della stessa. Ci sono stati molti ostacoli sulla strada verso la soluzione finale, ma siamo riusciti a superarli con successo", afferma Schiesling.
La sicurezza ha la priorità
Per il serraggio interno, Hainbuch ha preso in considerazione anche la possibilità di sostituire individualmente le bussole di serraggio a segmenti e le battute di appoggio. Ma dopo aver valutato gli aspetti inerenti alla sicurezza, precisione e contaminazione, confrontando diversi approcci, è stato chiaro che un processo sicuro poteva essere ottenuto solo con mandrini pre-attrezzati. Ora, la cella di rettifica e la cella di tornitura/fresatura dispongono ciascuna di dieci mandrini ad espansione MAXXOS con interfaccia di cambio rapido centroteX AC. Questi mandrini sono stoccati in magazzini con la configurazione corrispondente ai diversi alloggiamenti e vengono sostituiti automaticamente dal robot.
Hainbuch ha più che soddisfatto le esigenze
Philipp Wußler, responsabile della divisione rettifica di WTO, inizialmente aveva forti dubbi sul fatto che tutto potesse funzionare: "Fortunatamente, queste incertezze sono svanite. I dispositivi di serraggio soddisfano tutti i requisiti, sia per quanto riguarda la pulizia, che la precisione e, cosa molto importante, la ripetibilità; infatti ad ogni cambio di mandrino, siamo entro i 3 µm richiesti", osserva soddisfatto Wußler. Il processo di produzione automatizzato ha ridotto i tempi di attrezzaggio del 25% rispetto al vecchio metodo, che prevedeva la sostituzione dei mandrini, e l'allineamento in modo manuale e griffe rettificate per garantire la precisione. "Anche gli scarti sono stati ridotti in modo significativo o sono quasi nulli. Questo perché il serraggio era meno preciso. Ora il serraggio viene effettuato attraverso l’effetto di tiro assiale contro la battuta ed è molto più preciso. Una volta eseguito il rodaggio del pezzo, sappiamo che il processo di attrezzaggio successivo funzionerà correttamente. Ciò significa che non avremo più problemi di dispositivi di serraggio", aggiunge Wußler. Per WTO è chiaro: se il serraggio è più sicuro, anche il processo è più sicuro.
I dipendenti sono ora solo nel centro di comando
"La Smart Factory è progettata in modo che l'unica operazione manuale sia la consegna della materia prima. Un sistema di trasporto senza conducente preleva anche gli alloggiamenti finiti, che vengono ispezionati e misurati nella cella di produzione, e li porta dalla macchina al magazzino. La Smart Factory comprende un centro di comando con uffici per la pianificazione dei processi produttivi e la programmazione. Anche i dispositivi di bloccaggio e la definizione dei parametri di movimentazione per l'automazione vengono pianificati lì", spiega Tschiggfrei. Sono già previsti altri progetti e Hainbuch fornirà nuovamente i dispositivi di serraggio e parteciperà al processo di avviamento. In conclusione, Tschiggfrei afferma che: "Siamo molto soddisfatti. Volevamo un partner che portasse avanti questo progetto di sviluppo insieme a noi. e Hainbuch si è impegnata al massimo per raggiungere l'ultimo "µm". I signori Schiesling e Wußler, in particolare, si sono dedicati con passione al progetto; ci vogliono persone così per realizzare con successo un piano ambizioso come questo. Dal mio punto di vista, il risultato è stato persino migliore del previsto".
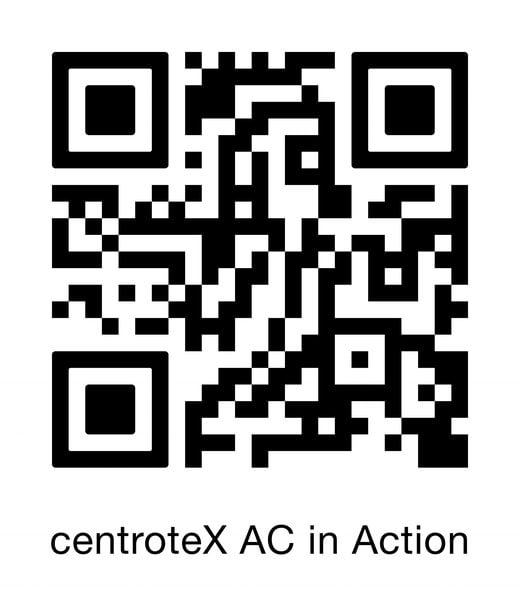
centroteX AC di HAINBUCH in azione e ulteriori informazioni sul prodotto
Cliente: WTO Werkzeug-Einrichtungen GmbH
WTO è un'azienda familiare di seconda generazione con 280 dipendenti, situata a Ohlsbach, che quest'anno festeggia il suo 40° anniversario. WTO è un pioniere nello sviluppo e nella produzione di portautensili di precisione statici e rotanti per centri di tornitura CNC. La Smart Factory, per la quale WTO ha investito 40 milioni di euro, sta definendo gli standard nella digitalizzazione e nell'automazione della produzione di piccole serie. Il nuovo edificio di 14.000 m² è composto da 9.000 m² dedicati alla Smart Factory e da un complesso di uffici di 5.000 m². La Smart Factory è anche progettata per la sostenibilità e viene alimentata con fonti di energia rinnovabili. È dotata di un impianto fotovoltaico e il calore di scarto del processo viene utilizzato per il riscaldamento, ciò comporta un risparmio di quasi 1.000 tonnellate di CO2 all'anno.
Da anni i costi di produzione si dirigono in una sola direzione, verso l'alto, mentre il mercato richiede costi di produzione sempre più bassi. Inoltre, c'è una mancanza di lavoratori qualificati. Queste sono le sfide con cui si confrontano quotidianamente molti produttori, tra cui WTO, un costruttore di portautensili di precisione statici e rotanti. La soluzione sembra ovvia: un capannone di produzione completamente automatizzato. La produzione in lotti è da sempre basata su metodi ben consolidati, ma per le piccole quantità è necessario sviluppare nuovi processi e integrarli in un sistema globale. Perché? Perché i dispositivi di serraggio, ad esempio, devono essere cambiati più volte al giorno, il che pone enormi sfide in termini di processo e sicurezza. In collaborazione con Hainbuch, produttore di tecnologie di bloccaggio di Marbach, WTO ha superato gli ostacoli eseguendo una serie di misurazioni e test strettamente coordinati. Nella nuova Smart Factory di WTO, tutti i processi sono automatizzati, con robot che inseriscono i componenti, cambiano i dispositivi di bloccaggio e sistemi di trasporto senza conducente che portano tutto da A a B. Dalla fine del 2022, la produzione di uno dei componenti degli strumenti guidati funziona autonomamente 24 ore su 24, 7 giorni su 7, in lotti da 1 a 100 pezzi. Si tratta di una pietra miliare per WTO e Hainbuch dopo una fase di sviluppo durata 3 anni.
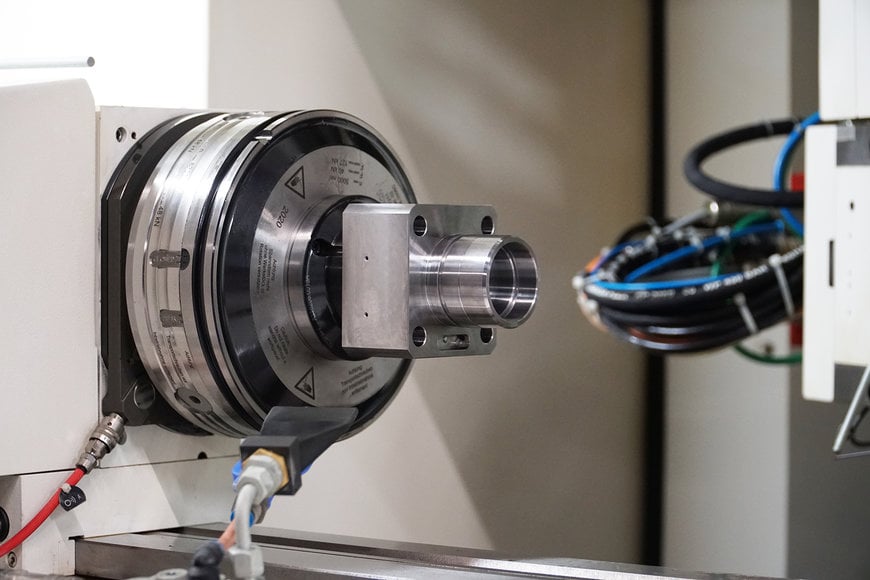
Il pezzo viene bloccato dall'interno su un mandrino ad espansione
La Smart Factory era l'unica soluzione
WTO ha sede a Ohlsbach, vicino a Offenburg, lontano dalle grandi città, dove c'è sempre più mancanza di lavoratori qualificati e, purtroppo, a causa degli sviluppi demografici, questa situazione è destinata a peggiorare. A questo si aggiunge anche il fatto che sempre meno persone vogliono diventare operatori di macchine e c'è sempre meno disponibilità a lavorare su turni. Sascha Tschiggfrei, amministratore delegato di WTO, ha riconosciuto questa situazione e nel 2016 ha iniziato a pensare a delle soluzioni. "I lavoratori qualificati sono una cosa, l'aumento dei costi è un'altra. Poiché operiamo a livello internazionale, la concorrenza è alta, infatti alcune aziende scelgono di trasferirsi all'estero dove i costi sono più bassi. Tuttavia, noi volevamo mantenere la nostra sede in Germania, quindi abbiamo dovuto reagire per assicurarci che la nostra azienda rimanesse competitiva sul lungo periodo. Il nostro futuro è la Smart Factory, che produce 24 ore su 24 e funziona in modo completamente automatico. Ci dà un vantaggio competitivo e ci permette anche di attrarre personale più qualificato", ha dichiarato Tschiggfrei.
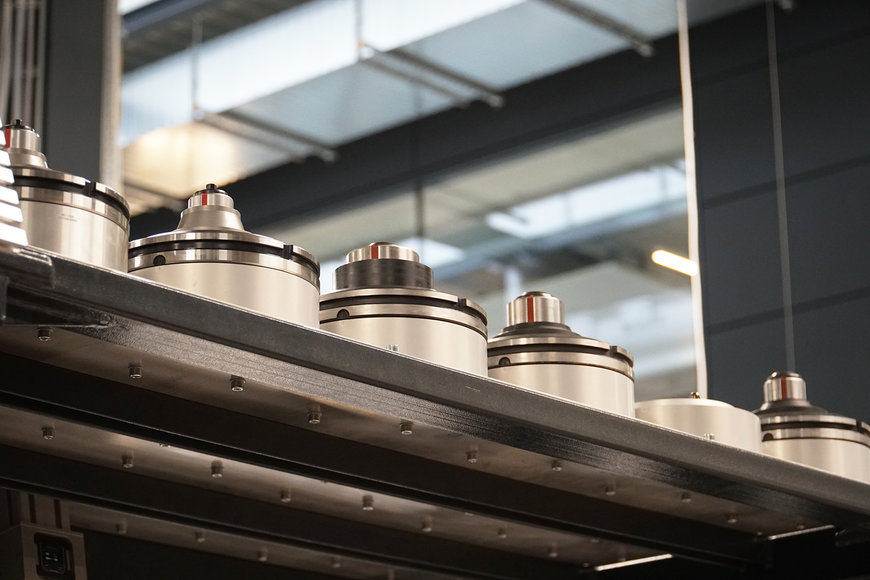
I mandrini pre-attrezzati sono pronti per il cambio automatico del dispositivo di serraggio
La ricerca di un partner esclusivo
Per questo progetto molto ambizioso, WTO voleva coinvolgere un partner esclusivo per le attrezzature di serraggio che, con impegno e competenza, potesse contribuire con una tecnologia adeguata. "Abbiamo elaborato i dettagli tecnici in team di progetto. Le domande erano: come possiamo bloccare i pezzi? Come possiamo automatizzare il bloccaggio? Come possiamo cambiare automaticamente i dispositivi di serraggio? L'obiettivo era che le macchine eseguissero i cambi completamente in autonomia. e ciò richiedeva dispositivi di serraggio che avessero questa capacità. Inoltre, avrebbero dovuto rispettare il processo di rettifica ad alta precisione che utilizziamo regolarmente, con una tolleranza massima di 3 µm", ha dichiarato Tschiggfrei. Una volta definito il concetto di Smart Factory, il passo successivo è stato quello di cercare un partner. Poiché WTO e Hainbuch avevano già collaborato con successo in vari progetti internazionali, Hainbuch è stata la prima scelta. Alla fine del 2019 sono iniziate le prime discussioni per definire i requisiti del dispositivo di bloccaggio e le proposte di design sviluppate da Hainbuch sono state accettate.
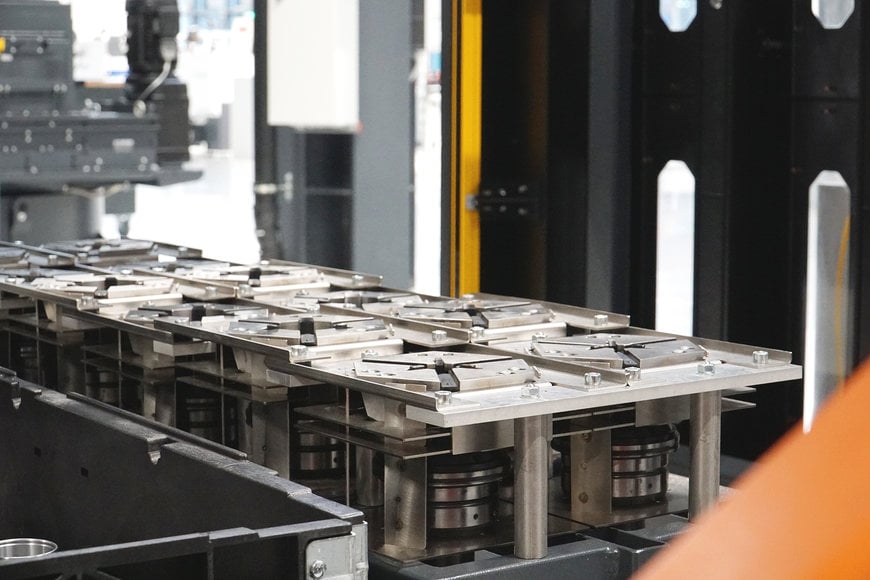
Per la produzione di diversi alloggiamenti, sono disponibili 18 set di serraggio, ciascuno composto da una pinza di serraggio con battuta d’appoggio
Pronti a partire
WTO dispone di un capannone di produzione con oltre 50 macchine CNC. Il serraggio su queste macchine veniva effettuato principalmente con mandrini a griffe e sia il cambio che l'allineamento per ogni postazione erano effettuati manualmente. Il primo processo di produzione completamente non presidiato implementato nella Smart Factory è stato la produzione di un alloggiamento, con una lavorazione soft seguita da una lavorazione hard. Tschiggfrei ha spiegato ulteriormente: "Le macchine della Smart Factory sono tutte nuove. Si tratta di macchine standard, ma adattate in modo specifico per consentire il cambio automatico dei dispositivi di serraggio mediante un robot". Hainbuch doveva equipaggiare quattro macchine con dispositivi di serraggio: due centri di tornitura/fresatura in una cella con bloccaggio interno sul contro-mandrino e due rettificatrici cilindriche in un'altra cella, una con bloccaggio esterno e una con bloccaggio interno. Per il serraggio esterno per la rettifica, Hainbuch disponeva già di un mandrino standard, il TOPlus AC 100 con effetto di tiro assiale. Per i vari alloggiamenti sono ora disponibili 18 set di bloccaggio, composti da una pinza di serraggio con battuta d’appoggio, che vengono sostituiti automaticamente nel mandrino. Tuttavia, per il serraggio del diametro interno durante la tornitura e la rettifica, è stato necessario uno sviluppo completamente nuovo. Ci si è basati sul mandrino ad espansione MAXXOS T211 esistente, e ne si è sviluppato uno speciale implementando i controlli di sicurezza.
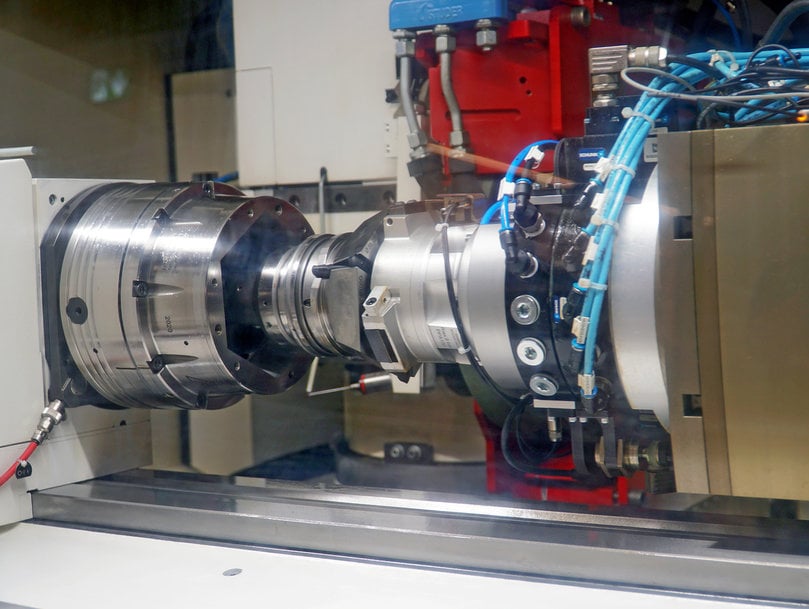
Rigorosi requisiti per i dispositivi di serraggio
Per Björn Schiesling, ingegnere progettista del reparto automazione di Hainbuch e che ha partecipato fin dall'inizio a questo nuovo progetto, ci sono dei requisiti fondamentali che devono essere considerati nell'automazione. "Cosa manca al cambio automatizzato dei dispositivi di bloccaggio? Il dipendente che pulisce le superfici di contatto. Anche le più piccole particelle di sporcizia causano una perdita di precisione. Poi ci sono i controlli di sicurezza: il mandrino può ruotare? È teso correttamente? È posizionato correttamente? È possibile che qualcosa si allenti? In generale, tutte cose che normalmente vengono controllate e regolate dall'operatore, ma con l'automazione non è più così. Per noi è stata una grande sfida implementare questi controlli nei dispositivi di serraggio. Naturalmente, abbiamo anche dovuto capire con il costruttore della macchina utensile come questo processo potesse essere implementato in termini di tecnologia di controllo, monitorando la posizione della corsa. Ad esempio, per il controllo attraverso il rilevamento dell'aria, abbiamo creato i canali nel dispositivo di bloccaggio in modo da poter implementare l’automazione, ma è stato il costruttore della macchina ad installare l'alimentazione dell'aria e i sensori che comunicano con il sistema di controllo della stessa. Ci sono stati molti ostacoli sulla strada verso la soluzione finale, ma siamo riusciti a superarli con successo", afferma Schiesling.
La sicurezza ha la priorità
Per il serraggio interno, Hainbuch ha preso in considerazione anche la possibilità di sostituire individualmente le bussole di serraggio a segmenti e le battute di appoggio. Ma dopo aver valutato gli aspetti inerenti alla sicurezza, precisione e contaminazione, confrontando diversi approcci, è stato chiaro che un processo sicuro poteva essere ottenuto solo con mandrini pre-attrezzati. Ora, la cella di rettifica e la cella di tornitura/fresatura dispongono ciascuna di dieci mandrini ad espansione MAXXOS con interfaccia di cambio rapido centroteX AC. Questi mandrini sono stoccati in magazzini con la configurazione corrispondente ai diversi alloggiamenti e vengono sostituiti automaticamente dal robot.
Hainbuch ha più che soddisfatto le esigenze
Philipp Wußler, responsabile della divisione rettifica di WTO, inizialmente aveva forti dubbi sul fatto che tutto potesse funzionare: "Fortunatamente, queste incertezze sono svanite. I dispositivi di serraggio soddisfano tutti i requisiti, sia per quanto riguarda la pulizia, che la precisione e, cosa molto importante, la ripetibilità; infatti ad ogni cambio di mandrino, siamo entro i 3 µm richiesti", osserva soddisfatto Wußler. Il processo di produzione automatizzato ha ridotto i tempi di attrezzaggio del 25% rispetto al vecchio metodo, che prevedeva la sostituzione dei mandrini, e l'allineamento in modo manuale e griffe rettificate per garantire la precisione. "Anche gli scarti sono stati ridotti in modo significativo o sono quasi nulli. Questo perché il serraggio era meno preciso. Ora il serraggio viene effettuato attraverso l’effetto di tiro assiale contro la battuta ed è molto più preciso. Una volta eseguito il rodaggio del pezzo, sappiamo che il processo di attrezzaggio successivo funzionerà correttamente. Ciò significa che non avremo più problemi di dispositivi di serraggio", aggiunge Wußler. Per WTO è chiaro: se il serraggio è più sicuro, anche il processo è più sicuro.
I dipendenti sono ora solo nel centro di comando
"La Smart Factory è progettata in modo che l'unica operazione manuale sia la consegna della materia prima. Un sistema di trasporto senza conducente preleva anche gli alloggiamenti finiti, che vengono ispezionati e misurati nella cella di produzione, e li porta dalla macchina al magazzino. La Smart Factory comprende un centro di comando con uffici per la pianificazione dei processi produttivi e la programmazione. Anche i dispositivi di bloccaggio e la definizione dei parametri di movimentazione per l'automazione vengono pianificati lì", spiega Tschiggfrei. Sono già previsti altri progetti e Hainbuch fornirà nuovamente i dispositivi di serraggio e parteciperà al processo di avviamento. In conclusione, Tschiggfrei afferma che: "Siamo molto soddisfatti. Volevamo un partner che portasse avanti questo progetto di sviluppo insieme a noi. e Hainbuch si è impegnata al massimo per raggiungere l'ultimo "µm". I signori Schiesling e Wußler, in particolare, si sono dedicati con passione al progetto; ci vogliono persone così per realizzare con successo un piano ambizioso come questo. Dal mio punto di vista, il risultato è stato persino migliore del previsto".
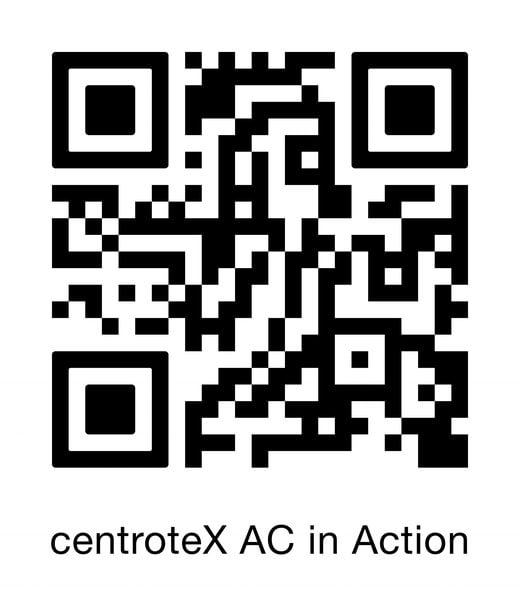
centroteX AC di HAINBUCH in azione e ulteriori informazioni sul prodotto
Cliente: WTO Werkzeug-Einrichtungen GmbH
WTO è un'azienda familiare di seconda generazione con 280 dipendenti, situata a Ohlsbach, che quest'anno festeggia il suo 40° anniversario. WTO è un pioniere nello sviluppo e nella produzione di portautensili di precisione statici e rotanti per centri di tornitura CNC. La Smart Factory, per la quale WTO ha investito 40 milioni di euro, sta definendo gli standard nella digitalizzazione e nell'automazione della produzione di piccole serie. Il nuovo edificio di 14.000 m² è composto da 9.000 m² dedicati alla Smart Factory e da un complesso di uffici di 5.000 m². La Smart Factory è anche progettata per la sostenibilità e viene alimentata con fonti di energia rinnovabili. È dotata di un impianto fotovoltaico e il calore di scarto del processo viene utilizzato per il riscaldamento, ciò comporta un risparmio di quasi 1.000 tonnellate di CO2 all'anno.
Richiedi maggiori informazioni…