www.industria-online.com
14
'20
Written on Modified on
LA PRIMA FABBRICA DI AUTO ELETTRICHE DELLA GERMANIA FISSA NUOVI PARAMETRI DI RIFERIMENTO
Il più grande produttore di automobili al mondo si prepara al futuro. Nei prossimi anni, Volkswagen si convertirà radicalmente alla mobilità elettrica e, in questo processo, lo stabilimento di Zwickau svolgerà un ruolo fondamentale. Con il modello ID.3 qui nasce il progetto per la nuova flotta elettrica. Ai blocchi di partenza, i professionisti della piegatura di Bystronic.
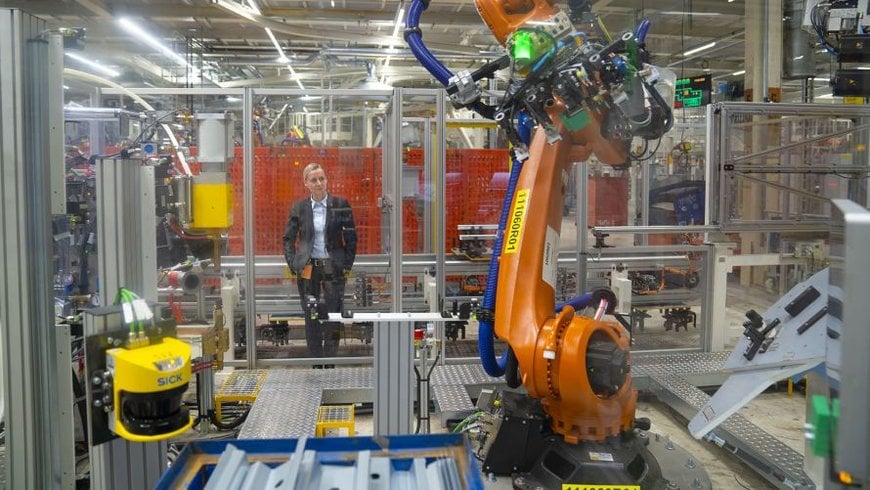
Nell'industria automobilistica molte cose accadono a porte chiuse. Lo stesso vale per il nuovo orientamento dei produttori verso la mobilità elettrica. Se però è Angela Merkel in persona a dare il via alla produzione della nuova VW ID.3, tutto acquisisce un carattere estremamente formale. Questo è quanto è avvenuto lo scorso novembre nella città sassone di Zwickau dove sono state avviate le linee di produzione per il progetto al momento più ambizioso di tutta l'industria automobilistica.
La ID.3 è più di un semplice nuovo modello: questo bolide incarna il futuro di VW e dovrà segnare una nuova era. Il Gruppo si è posto l'obiettivo di diventare il produttore leader a livello globale di veicoli elettrici. E questa ambizione è già di per sé esplicativa. Mediante investimenti di 1,2 miliardi di euro, VW intende rendere lo stabilimento di Zwickau la più grande fabbrica di mobilità elettrica d'Europa. Nel 2021 dovranno già uscire dalle sue linee oltre 300.000 auto elettriche.
Una piattaforma per tutta la famiglia
Finora le vendite di veicoli elettrici sono avanzate solo a rilento. La ID.3 intende cambiare questa situazione, grazie a un prezzo interessante inferiore ai 30.000 euro, un tempo di carica rapido e un'autonomia fino a 550 chilometri. Il presidente del Marchio Jürgen Stackmann promette: «Avrà esterni delle dimensioni di una Golf, gli interni di una Passat e l'accelerazione di una GTI.» A quanto pare, le promesse sono giunte alla clientela: oltre 30.000 vetture sono già state prenotate e verranno consegnate quest'anno.
La ID.3 getta le basi per una generazione di vetture a emissioni zero, dal SUV T-Cross al Bulli. La piattaforma modulare per veicoli elettrici (in breve MEB) garantisce la necessaria scalabilità: entro il 2022 verrà infatti utilizzata in 27 modelli di quattro marchi del Gruppo. Il prototipo «ID.R Pikes Peak» ha già dimostrato che, in questo ambito, non esistono confini. Il 24 giugno 2018, in occasione dell'omonima gara in salita negli USA, la supersportiva con la sua trazione integrale elettrica da 680 CV ha scritto la storia del Motorsport superando di gran lunga il record originario della leggenda del rally Sebastien Loeb. Questa supersportiva rimarrà un sogno da circuito ma dimostra ciò che la trazione elettrica di VW è in grado di fare.
Un tempo di ciclo di 76 secondi
Kati Langer si trova nel padiglione produttivo n. 12. Sta ispezionando la Xpert 40, collegata alla cella di produzione con i due robot Kuka. La appassionata venditrice di Bystronic, impegnata nel progetto ID.3 con VW sin dall'inizio, è visibilmente orgogliosa del sistema. «Per integrare senza problemi i sistemi di piegatura nella produzione di VW, abbiamo dovuto superare alcune sfide strutturali», ha affermato mentre osserviamo i due robot di piegatura al lavoro.
Il primo robot preleva il pezzo dalla stazione dei contenitori e lo deposita nel sistema di centraggio. Il secondo robot lo inserisce rapidamente nella pressa piegatrice e svolge le prime due operazioni di piegatura. Dopodiché riporta il pezzo nel sistema di centraggio e il robot numero uno esegue i processi di piegatura rimanenti. Successivamente, in un sistema fisso vengono saldati due dadi sferici. Infine, il braccio della pinza preleva il pezzo e lo colloca sul nastro trasportatore.
Questo processo dura esattamente 76 secondi. È un vero piacere osservare come i robot completano le loro sequenze di piegatura. Se non lo si vedesse con i propri occhi, non si potrebbe credere all'eleganza e all'agilità con cui i due robot lavorano fianco a fianco – o meglio pinza a pinza. Il pezzo piegato viene poi montato nella struttura di sostegno del telaio e serve a stabilizzare la sottostruttura. Una seconda cella di piegatura completamente automatica modella un pezzo che successivamente viene montato sul lato anteriore del telaio.
www.bystronic.com
Richiedi maggiori informazioni…