Trasparenza del processo inclusa
I sistemi di monitoraggio delle condizioni (CMS) rilevano i cambiamenti e le anomalie nel processo di produzione. Forniscono un allarme tempestivo dei danni incipienti, rilevano le deviazioni di qualità, monitorano la stabilità di un processo di produzione e assicurano un controllo di qualità costante in tutte le fasi della produzione e della creazione di valore. In questo contesto, i sistemi di presa e i dispositivi di serraggio assumono un'importanza sempre maggiore a causa della loro posizione più vicina al pezzo.
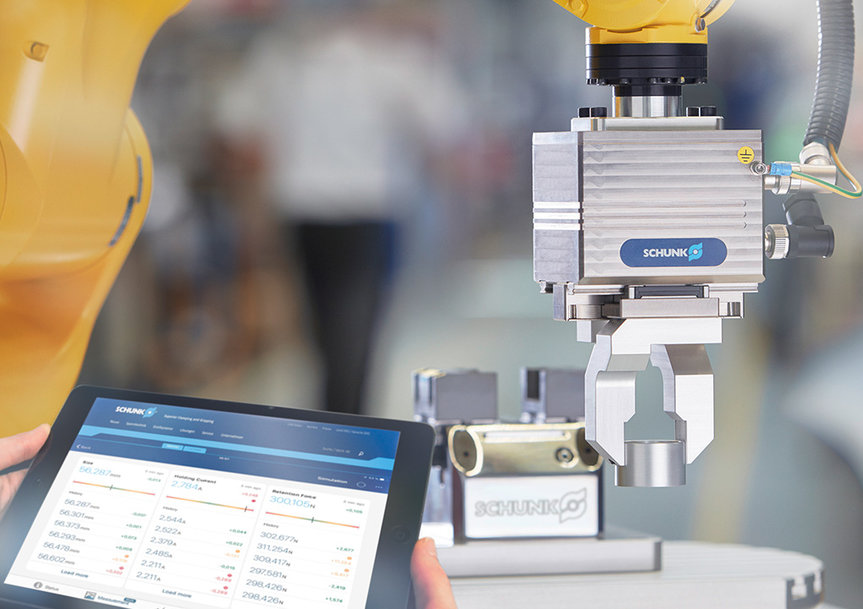
Non solo la lettura dei dati, ma anche l'analisi dei dati
Esiste già un'enorme quantità di dati generati dalle macchine e dai sistemi automatizzati, dagli utensili intelligenti e dai componenti che si trovano nelle fabbriche delle aziende manifatturiere. Tuttavia, solo una piccolissima parte di questi dati viene effettivamente utilizzata - le stime suggeriscono solo il cinque per cento circa. I valori registrati dai sensori sono stati finora poco significativi, al massimo sono stati utilizzati in caso di danni o per la ricerca di guasti. Utilizzando questi dati esistenti in modo completo, sistematico e soprattutto in tempo reale, è possibile realizzare scenari di produzione intelligente che promettono vantaggi sostanziali. Allo stesso tempo, il grado di connettività in rete e di digitalizzazione è anche associato a un rapido aumento della quantità di dati generati, il che significa che può sussistere il rischio che le connessioni ai data center nel cloud non siano in grado di far fronte agli immensi flussi di dati in rapida crescita e che si verifichino tempi di inattività e periodi di latenza elevati. Per questo motivo gli attuali progetti di ricerca si concentrano su un cambiamento fondamentale nel modo in cui i dati vengono intesi. Non ruotano più intorno alla semplice raccolta di dati come avveniva in precedenza, ma all'analisi dei dati in loco e alla loro conversione in informazioni preziose. L'attenzione principale è rivolta a come affinare i big data in dati intelligenti. Ad esempio, è necessario preparare informazioni sul corretto funzionamento di un sistema automatizzato e sul suo collegamento ideale con le azioni raccomandate.
Test integrato dei componenti
Ciò consente di controllare le caratteristiche di qualità dei componenti durante la manipolazione e di prendere decisioni OK/Non OK direttamente nella pinza. I dati registrati nella pinza di presa vengono pre-processati e analizzati nei componenti in tempo reale in modo che vengano attivate le risposte appropriate. Si riduce la mole di dati da trasferire ai soli dati utili come parametri significativi o indicatori chiave di performance (KPI). Oltre alle statistiche standard sui tempi di inattività, i KPI più importanti sono gli indici di capacità di processo (Cp) derivanti dall'analisi statistica del processo e l'efficienza di utilizzo del sistema automatizzato nel suo complesso. Si misurano tre tipi di dati di performance e si utilizzano metodi moltiplicativi per fonderli in un indicatore di produttività globale, l'efficienza totale del sistema automatizzato o l'efficacia complessiva delle apparecchiature (OEE).
L'efficienza totale del sistema automatizzato come indicatore chiave
Tre fattori sono rilevanti per la determinazione dell'OEE:
- Grado di prestazione (LG): Il grado di prestazione è una misura della velocità di lavorazione di un sistema di produzione. Questo si basa sui tempi di ciclo necessari per ottenere pezzi conformi o sulla capacità produttiva (M). Il grado di prestazione è indicato sotto forma di tempi di ciclo e quantità.
Quantità: LG = Mreale/Mpiano x 100%
- Grado di utilizzo (NG, disponibilità): Il grado di utilizzo è una misura della capacità di un sistema di produzione di eseguire con successo una funzione richiesta nel momento richiesto. Questo viene determinato in base ai tempi di funzionamento, al tasso di inattività λ, al tempo medio tra i guasti (MTBF) e al tempo medio di inattività (MDT). Quest'ultimo comprende diversi fattori come il tempo di manutenzione TW e il tempo di riparazione (tempo medio di riparazione, MTTR).
L'affidabilità indica la probabilità di non avere tempi di fermo macchina che influenzeranno la funzionalità di un'unità durante un certo periodo. Questo è determinato dal tasso di tempo di inattività degli elementi tecnici e quantificato dal periodo medio senza tempi di inattività (tempo di funzionamento), il "Tempo medio tra i guasti" (MTBF).
- Prestazioni di qualità (resa, ...): La prestazione di qualità è la misura della capacità di un sistema di produzione di assemblare/verificare entro le specifiche prescritte. I metodi di valutazione statistica della qualità sono utilizzati per analizzare e valutare il comportamento qualitativo dei processi di produzione. Le informazioni di campionamento vengono utilizzate per cercare di ottenere informazioni sul comportamento del tempo di distribuzione, ad esempio nel processo di assemblaggio. I risultati di questa analisi sono i calcoli della "capacità della macchina a breve termine" (potenziale macchina Cm, Cmk), della "capacità di processo preliminare" (potenziale processo preliminare Pp, Ppk) e della "capacità di processo a lungo termine" (potenziale processo a lungo termine Cp, Cpk).
La capacità della macchina è una misura della varianza caratteristica a breve termine proveniente dalla macchina.
La capacità di processo è una misura significativa della stabilità di un processo. Indica se un processo è in grado di soddisfare i requisiti stabiliti. In questi casi si parla di processi di produzione controllabili. Allo stesso tempo, fornisce anche una visione del comportamento a lungo termine del sistema complessivo nelle condizioni generali prevalenti (esseri umani, macchine, metodi, ambienti di lavoro). La capacità di processo identifica la capacità di una macchina o di un processo di ottenere caratteristiche specifiche con una distribuzione di frequenza che rientra nelle tolleranze richieste. A questo scopo, si crea la relazione tra la distribuzione statistica di una caratteristica di qualità misurabile e il campo di tolleranza specificato per questa caratteristica. I parametri di capacità di processo sono molto sensibili ai cambiamenti e agli sviluppi delle tendenze. Ciò significa che sono particolarmente adatti per le previsioni a medio termine e la manutenzione predittiva.
La pinza come abilitatore universale per una produzione intelligente e flessibile
I moduli di gestione intelligente creano facilmente le precondizioni necessarie per la piena integrazione dei sistemi di produzione automatizzata negli ambienti di produzione e aprono la possibilità di connessioni ad ecosistemi basati su cloud per determinare l'efficacia complessiva del sistema automatizzato (OEE), le statistiche dei tempi di inattività (MTBF, MTTR) e la stabilità di processo a medio termine utilizzando i parametri di capacità determinati. Uno di questi componenti chiave è la pinza parallela SCHUNK EGL, un modulo di presa standard intelligente che include funzioni standard integrate, un'interfaccia Profinet certificata ed elettronica integrata con corsa variabile ed una forza di presa impostabile tra 50 N e 600 N. Come sistema di misura in linea, per la "presa intelligente" la pinza intelligente utilizza la sua posizione esposta direttamente sul pezzo per ottenere dati e valutarli immediatamente utilizzando la tecnologia edge integrata nella pinza. Ciascuna singola fase del processo è monitorabile dettagliatamente e, per esempio, trasmessa al sistema di controllo, al sistema ERP di livello superiore nonché ai database analitici e alle soluzioni cloud. In questo modo la pinza intelligente è in grado di catturare ed elaborare informazioni sistematiche sul componente oggetto della presa, sul processo e sui componenti e reagisce adeguatamente. Consente di eseguire un controllo di qualità a circuito chiuso e il monitoraggio diretto del processo di produzione nel ciclo di produzione.
Rilevamento proattivo delle tendenze
La determinazione continua in tempo reale della capacità di processo a lungo termine (Cpk) per il rilevamento proattivo delle tendenze e la diagnosi degli errori ha dimostrato ottimi risultati con la pinza. Le correzioni di controllo introdotte vengono già applicate prima di raggiungere i limiti delle specifiche e consentono un controllo di processo significativamente più stabile. La fusione di sensori consente di utilizzare in parallelo diversi sensori e di analizzare successivamente i loro valori di misurazione per controllare e valutare gli stati attuali del sistema della presa nonché la situazione di accesso della presa. In questo modo è possibile differenziare gli oggetti di presa e rilevare i malfunzionamenti nella sequenza di produzione, come ad esempio le diverse qualità delle materie prime, l'usura degli utensili, gli scostamenti di tolleranza o i colli di bottiglia dei materiali. Utilizzando l'analisi del processo in tempo reale, le tendenze possono essere valutate e incluse immediatamente nel controllo qualità del flusso di produzione, ad esempio sulla base dei valori caratteristici della competenza. Le analisi di correlazione consentono inoltre di individuare contesti complessi e di eliminare più rapidamente pattern di errore complessi.
Intelligenza artificiale
In futuro, SCHUNK prevede di automatizzare le attività per il controllo dell'intera catena cinematica, composta da robot e pinze, nonché il monitoraggio del loro funzionamento, senza richiedere la programmazione di ogni singolo passo o dover impostare soglie e regolarle continuamente. L'utilizzo di metodi di intelligenza artificiale (AI) e l'utilizzo di diversi sensori sarà cruciale per questo tipo di sistemi di presa autonomi. In un'applicazione pilota, ad esempio, sono stati utilizzati metodi di intelligenza cognitiva per identificare i pezzi disposti in modo casuale con una telecamera e poi afferrarli autonomamente da un contenitore e guidarli nel loro processo di lavorazione. Allo stesso tempo, le deviazioni dagli eventi normali (le cosiddette anomalie) e dalle tendenze, come la deriva dei parametri di processo rilevanti, vengono apprese e utilizzate per affinare gli strumenti diagnostici nella pinza di presa, senza la necessità di interruzioni operative o di un eccessivo addestramento durante l'impostazione del sistema. Lo scopo della pinza non è solo quello di afferrare, ma anche di partecipare alla pianificazione totale, di monitorare l'intero processo utilizzando sensori e di analizzarlo continuamente. Qui, l'edge e il cloud computing sono complementari e vantaggiosi.
Portautensili con sensori
Dotato di un sensore, di una batteria e di un trasmettitore, il portautensili SCHUNK iTENDO monitora il processo a 5.000 Hz direttamente sull'utensile. Un algoritmo determina continuamente un parametro per la stabilità dei processi. Il valore IFT è stato sviluppato in particolare per iTENDO, ed esprime la vibrazione misurata con un valore numerico su una scala di intensità definita, analoga alla scala Richter utilizzata per i terremoti. Se il taglio diventa instabile, il sistema intelligente integrato interviene direttamente in tempo reale con una latenza di circa 20 ms e senza alcun intervento da parte dell'operatore. A seconda della situazione, il processo viene poi arrestato, ridotto o adattato ai parametri di base precedentemente definiti, l'alimentazione degli utensili modificati, gli utensili gemelli sostituiti o i messaggi inviati all'operatore. In funzione della specifica applicazione, un web service può essere utilizzato per definire sia i limiti precisi sia le reazioni corrispondenti, se superati. Nel medio termine, i componenti intelligenti consentiranno valutazioni statistiche, come l'efficacia globale delle apparecchiature (OEE), la capacità di processo (Cpk), il tempo medio tra guasti (MTBF), o sviluppi di tendenza come la deriva dei parametri o i gradienti dei tassi di guasto.
www.schunk.com
Richiedi maggiori informazioni…