www.industria-online.com
28
'10
Written on Modified on
Apparecchiature Verlinde per NZ Steel
KraneQuip, distributore Verlinde in Nuova Zelanda, è stato sfidato a trovare una soluzione razionale per progettare e costruire un carroponte da 16 tonnellate di portato in uno spazio limitato presso NZ Steel.
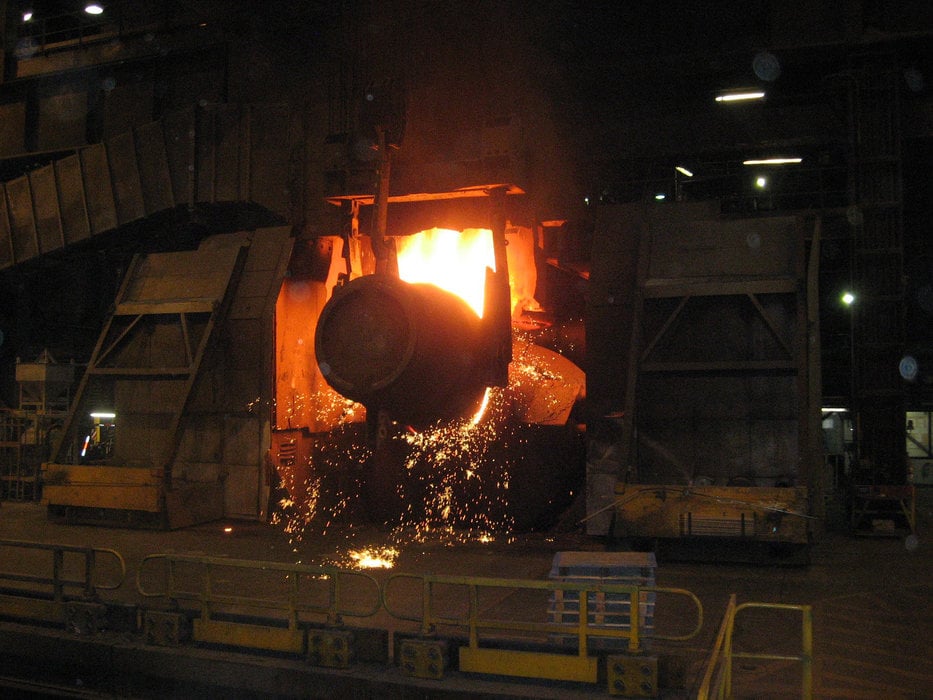
Il primo problema da affrontare era lo spazio disponibile nel quale inserire il carroponte. "Si è trattato di una grande sfida inserirlo in uno spazio di quattro metri di larghezza. Soprattutto considerando un'altezza di sollevamento di 30 metri - ha fatto notare Cobus Van der Walt, che ha aggiunto - e normalmente in questi casi è necessario utilizzare un paranco a cavo, con un tamburo sufficientemente ampio per poter contenere i 30 metri di cavo necessari per un sollevamento di tale portata, il che corrispondeva in pratica ad un elemento delle dimensioni dello spazio disponibile". Il carico puntuale doveva essere spostato da est ad ovest sulla trave del ponte, ma un paranco a cavo non era proponibile per via delle dimensioni. "Ci siamo quindi orientati sui paranchi a catena. Ma il problema con i verricelli a catena è che non ne esistono superiori alle cinque tonnellate o a 7,5 tonnellate per quanto ci riguarda, dato che il nostro fornitore, Verlinde, poteva costruirne uno di tale portata. Eravamo tuttavia ben lontani dalle 16 tonnellate richieste". Dopo aver molto riflettuto, il team KraneQuip ha suggerito di utilizzare due paranchi a catena della portata di dieci tonnellate l'uno. In pratica, però, si dovevano abbinare due cavi da cinque tonnellate per ottenere dieci tonnellate per gruppo e occorreva poi sistemare due di questi gruppi sulla trave del carroponte.
"Alcune settimane più tardi, grazie alle notevoli capacità progettuali, siamo riusciti ad installare i verricelli su una trave di carroponte monorotaia per soddisfare le esigenze di carico puntuale da movimentare. Per ottenere ciò abbiamo dovuto modificare la progettazione dei puntoni, avendo a disposizione solo pochi millimetri".
Un'altra sfida consisteva nel progettare un carroponte in grado di sostenere 16 tonnellate. Non bastava la più efficiente delle travi, quella diritta standard, mentre una trave scatolata sarebbe stata troppo costosa. Pertanto, KraneQuip ha dovuto progettare un ponte a trave diritta con rinforzi superiori e staffe inferiori per assorbire il carico. In tal modo, il team ha ridotto i tempi d'esecuzione e fatto risparmiare a NZ Steel i maggiori costi derivanti dalla fabbricazione di una trave scatolata.
Un ulteriore problema è stato posto dalla dimensione esterna dei carter proteggicatena. I due gruppi di paranchi, anche se perfettamente idonei, non potevano avvicinarsi sufficientemente l'un l'altro per soddisfare le distanze di avvicinamento est-ovest richieste. Si è reso pertanto necessario modificare i due carter proteggicatena centrali. "Non potevamo abbassarci oltre perché non c'era spazio disponibile, abbiamo quindi deciso di sfruttare la larghezza", ha ammesso Cobus van der Walt. A questo punto si è presentato un altro problema, nel senso che la catena doveva occupare tutta la larghezza dei carter. Il team ha dovuto installare delle piastre deflettrici al centro ed aprire la gola del carter per consentire alla catena di distribuirsi correttamente al suo interno. Il primo tentativo è andato a vuoto ma dopo diverse modifiche le cose sono andate a posto.
Al momento della messa in funzione si è dovuto procedere a numerose regolazioni per garantire la traslazione identica dei due ganci alla stessa altezza e la contemporanea attivazione dei commutatori sui puntoni. Sono insorte numerose difficoltà con la velocità di spostamento nel senso della lunghezza, perché la gru poteva muoversi in tutte le direzioni solamente a bassa velocità. Per risolvere il problema sono stati utilizzati comandi di velocità variabile. Però, durante lo spostamento nel senso della lunghezza, si accumulava molta sporcizia sulle rotaie e le ruote risultavano essere troppo larghe per poter assorbire il carico dell'intera gru e quello massimo di lavoro di sicurezza. La potenza a bassa velocità era appena sufficiente per muovere la gru e la sporcizia ha provocato anche dei blocchi. Alla fine è stato deciso che l'unica cosa da fare era eliminare completamente la sporcizia dalle rotaie ogni volta prima dell'uso.
"Questo progetto ha costituito per il team KraneQuip una sfida senza precedenti e siamo decisamente soddisfatti d'averla potuta superare - ha dichiarato Cobus van der Walt, il quale ha aggiunto - È stato veramente esaltante poter rispondere alle esigenze molto specifiche di NZ Steel, anche se poteva sembrare impossibile!"
Richiedi maggiori informazioni…